Why construction equipment maintenance matters
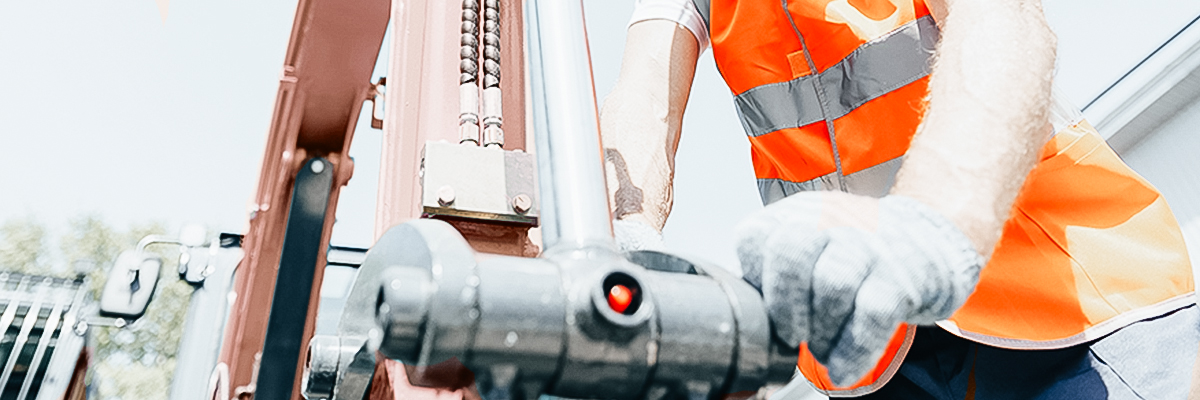
All equipment used on construction sites is built to withstand the toughest working environments. However, regular maintenance is required to ensure that construction equipment remains in top condition. Sticking to a schedule of both routine and preventive maintenance not only prolongs the life of small earth-movers, mobile elevating work platforms (MEWPs) and telehandlers, but also provides other benefits.
Types of maintenance
Routine maintenance
The first type of maintenance that is indispensable to keep construction equipment going is regular routine maintenance. Routine maintenance can be carried out by a service technician or by the machine operator. It includes the visual inspection and monitoring of vital machine components, for example:
- General safety inspections;
- Inspection of tracks and undercarriage parts;
- Pressure test of tyres;
- Checking transmission fluid and engine coolant levels;
- Filter changes;
- Etc.
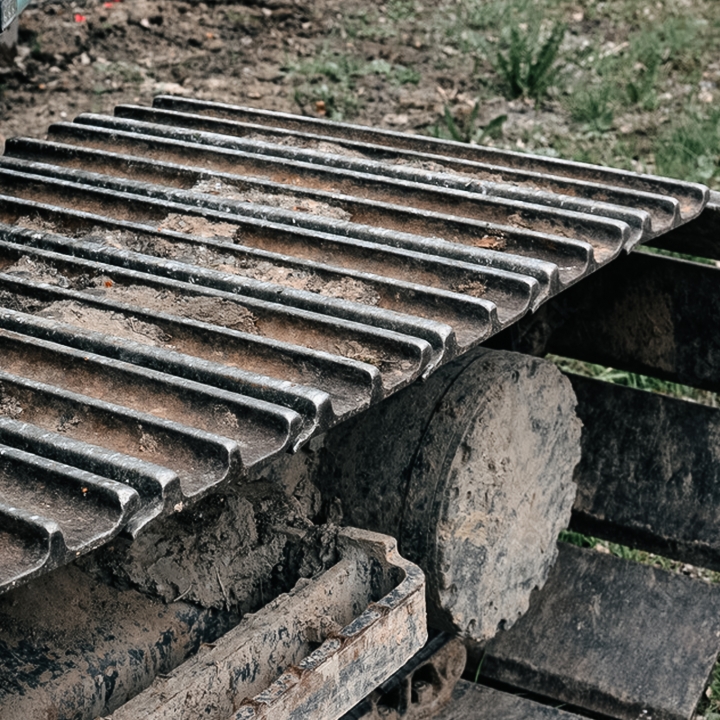
Preventive maintenance
In addition to routine maintenance, it is also important to regularly schedule preventive maintenance. This type of maintenance is a bit more elaborate because it takes a big-picture approach. Rather than being forced to service a small earth-mover, MEWP or telehandler due to a breakdown, the technician or repairer looks for problems in the making. In other words, preventive maintenance is carried out to help prevent machine breakdowns.
If the inspection shows that a particular part is worn out, then replacement is in order. For some parts such as tyres and tracks, it is easier to tell when they need replacing because they show telltale signs of wear. However, it is always best to consult the machine’s service manual, as this document contains the manufacturer’s guidelines on how much wear is acceptable for certain components.
The benefits of regular maintenance
Naturally, there are a number of benefits to regular maintenance of construction equipment:
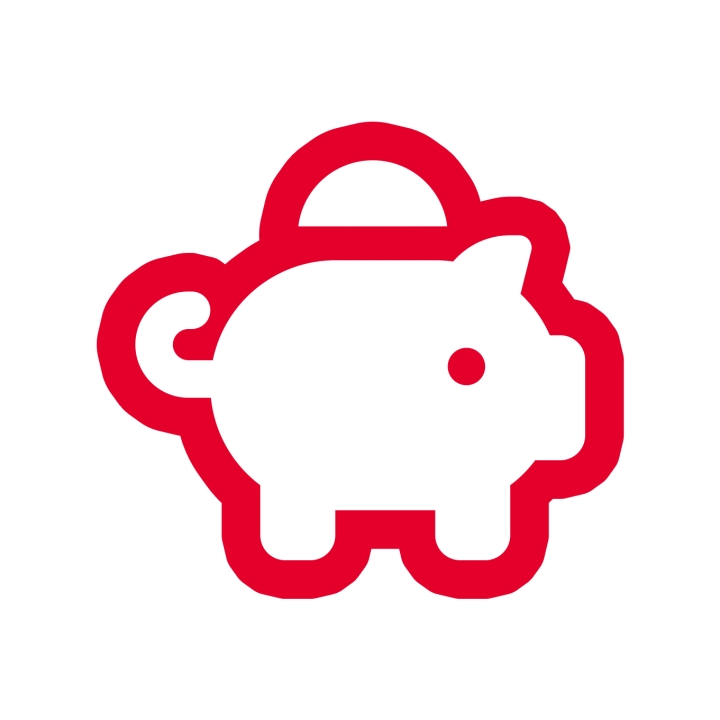
1. Save money
Perhaps one of the most important benefits is that investing in maintenance saves money in the long run because of various reasons. First of all, regular maintenance ensures that defects are detected early and long before they become a really expensive issue. For example, it is much cheaper to make a small repair and replace one engine component than to replace the whole engine if the problem had gone undetected.
Secondly, regular maintenance ensures that unexpected machine breakdowns can generally be avoided. This means the machine is not at a standstill while waiting for the replacement part to arrive and there is no loss of revenue for the company. And finally, but not unimportantly, well-maintained machines have a higher resale value.
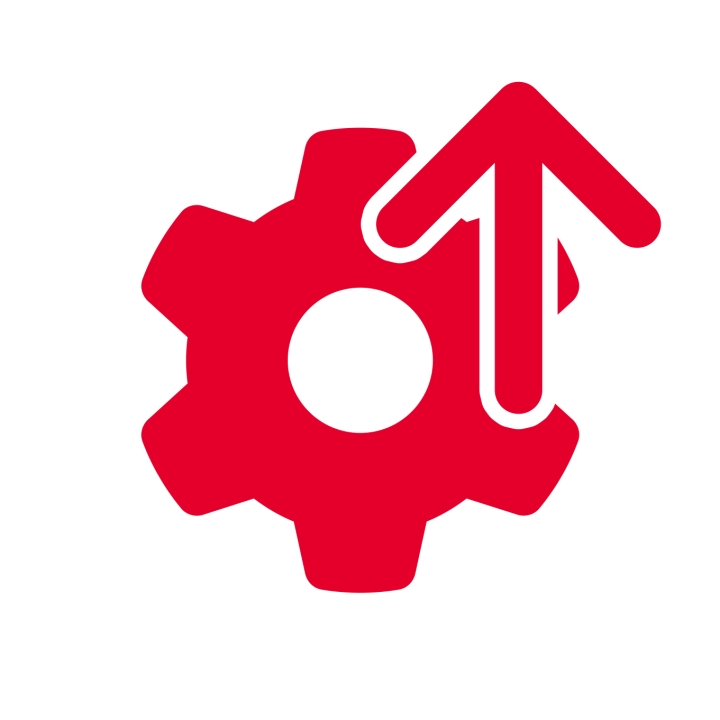
2. Improve machine efficiency
Well-maintained construction equipment not only lasts longer but also works better and more efficiently, resulting in higher productivity. In addition, if no machine has to remain on the sidelines because of a breakdown, then the business itself can run more efficiently as well.
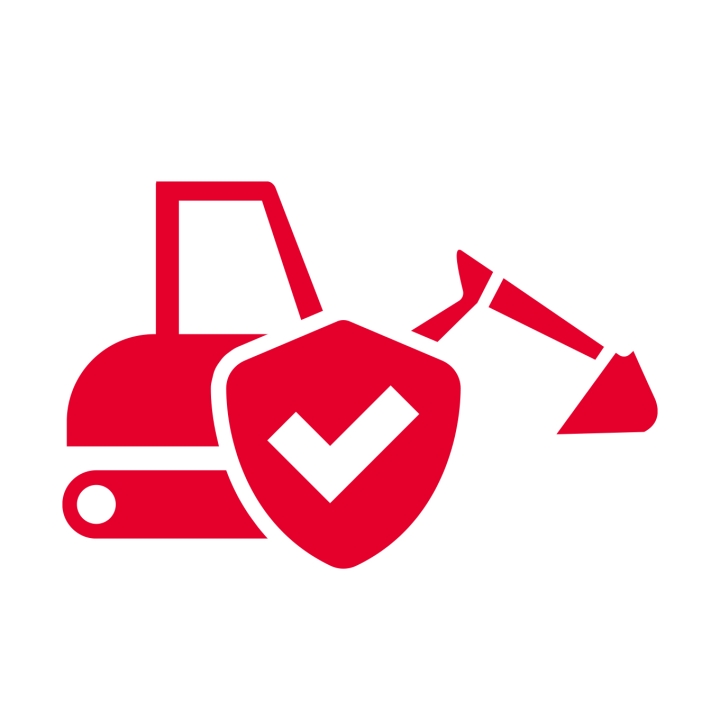
3. Increase safety
Another benefit of maintenance is that a small earth-mover, mobile elevating work platform or telehandler in top condition is safer and more reliable. Even a small defect could lead to an unsafe situation that turns out catastrophic for the operator and those working in close proximity to the machine. Furthermore, a sudden breakdown could even cause damage to other machines in the vicinity. So better safe than sorry.
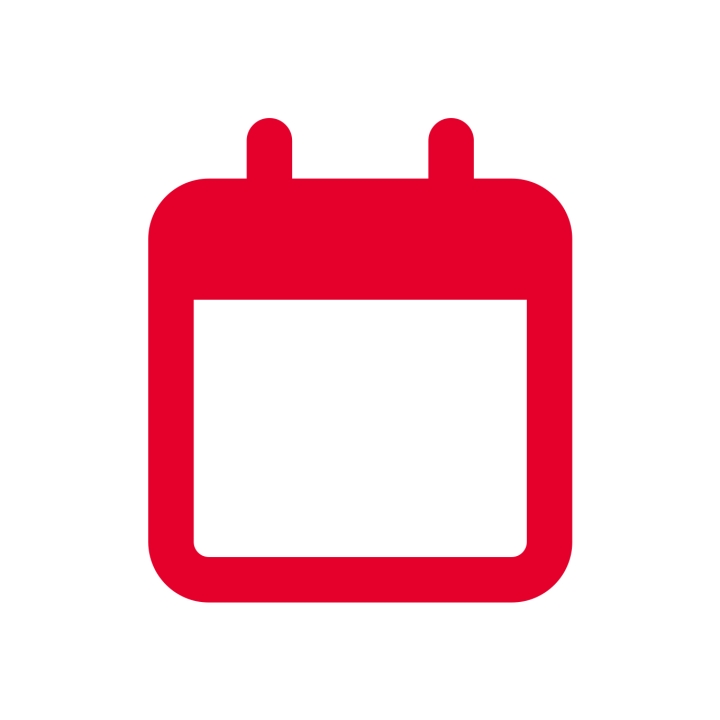
Creating a schedule
A clear and fixed schedule makes or breaks machine maintenance. To ensure that maintenance schedules are adhered to, it is important to have a clear overview of what needs to be done and when. The specific maintenance interval can be determined in a number of ways:
- Operating hours (e.g. after 500 hours of use);
- Distance travelled (e.g. every 2,000 km);
- Length of time (e.g. every first Monday of the month).
Which one of these three is best depends on the type of machine and the manufacturer’s guidelines. However, it is also advisable to take into account local climate conditions – such as heavy rain, snow, temperature fluctuations … – when drawing up a maintenance schedule.
Documentation is key
Scheduling routine and preventive maintenance is all well and good, but it means nothing if it is not well documented. It is vital to keep track of when the equipment has been serviced, what was found during maintenance and what actions were taken.
Looking for parts?
- Click here to check out our full parts range for construction equipment.
- Visit our online shop to order parts and accessories for small earth-movers, mobile elevating work platforms and telehandlers.
- Please feel free to contact us if you have any other questions.
You may also be interested in the following blogs
About the authors
This blog post is brought to you by your construction equipment marketing team.
Request your customer account to shop parts online
Submit the application form to specify your business needs and request your customer account.
Our sales team will contact you within 3 business days to talk about your business needs and complete registration.
After your account is set up, you will receive a personal login to our online shop. We will guide you in finding parts and placing your first order.
Request your account
Over 75.000 customers trust TVH as their spare parts supplier to ensure their client’s equipment fleet is running smoothly and efficiently. It starts with a customer account.